
Total Quality Management
Q1. Explain why continual quality improvement is important.
ANS: Continual improvement is fundamental to success in the global marketplace. A company that is just maintaining the status quo in such key areas as quality, new product development, adoption of new technologies, and process performance is like a runner who is standing still in a race. Customer needs are not static; they change continually.
A special product feature that is considered innovative today will be considered just routine tomorrow. A product cost that is considered a bargain today will be too high to compete tomorrow. A good case in point in this regard is the ever-falling price for each new feature introduced in the personal computer. The only way a company can hope to compete in the modern marketplace is to improve continually.
Q2. What is management’s role in continual quality improvement?
ANS: The picture of a company reaping big rewards through quality improvement is incomplete unless it includes some realities that have been unwelcome to most upper managers. Chief among these realities is the fact that the upper managers must participate personally and extensively in the effort. It is not enough to establish policies, create awareness, and then leave all else to subordinates. That has been tried, over and over again, with disappointing results (Juran on Leadership for Quality).
Management can play the necessary leadership role—and that essentially is its role—in continual improvement by doing the following:
-
Establishing an organization-wide quality council and serving on it.
-
Working with the quality council to establish specific quality improvement goals with timetables and target dates.
-
Providing the necessary moral and physical support. Moral support manifests itself as commitment. Physical support comes in the form of the resources needed to accomplish the quality improvement objectives.
-
Scheduling periodic progress reviews and giving recognition where it is deserved.
-
Building continual quality improvement into the regular reward system, including promotions and pay increases.
Q3. Discuss the Kaizen approach.
ANS: The underlying value system of Kaizen can be summarized as continual improvement of all things, at all levels, all the time, forever. All of the strategies for achieving this fall under the Kaizen umbrella (see figure below). Executive managers, middle managers, supervisors, and line employees all play key roles in implementing Kaizen.
The Five-Step Plan is the Japanese approach to implementing Kaizen:
Step 1: Straighten up. This step involves separating the necessary from the unnecessary and getting rid of the unnecessary in such areas as tools, work in process, machinery, products, papers, and documents.
Step 2: Put things in order. This step involves putting such things as tools and material in their proper place and keeping things in order so that employees can always find what they need to do the job without wasting time looking.
Step 3: Clean up. This step involves keeping the workplace clean so that work can proceed in an efficient manner, free of the problems that can result when the work site is messy.
Step 4: Standardize. This step was originally aimed at standardizing how the first three of the Five-S’s were implemented and maintained, but since then expanded to include standardizing on best practices. Visual management is also a major component of standardization.
Step 5: Discipline. This step involves careful adherence to standardized work procedures. This requires discipline.
Q4. How would you describe a lean system?
ANS: Lean was originally developed as a manufacturing concept and, as such, is often referred to as lean manufacturing. However, as has happened with so many quality management– related concepts, the service sector—impressed with the results enjoyed by practitioners of lean manufacturing— began to adopt and adapt the concept to this sector. Consequently, we use the term Lean in this text to convey the message that the concept can be applied with good results in the manufacturing and service sectors. The purpose of adopting Lean as a business improvement method is to produce better products or deliver better services using fewer resources. If the concept had a motto, it would be this: doing more with less and doing it better.
Q5. What is lean six-sigma and how would you apply it to a quality management system?
ANS: Lean Six Sigma is nothing more or less than the marriage of Lean and Six Sigma. The objective of Lean Six Sigma is to make the organization superior in its day-to-day work and processes, its products and services, and its business results. This has also been the objective of many organizations that have found that Lean alone, or Six Sigma by itself, did not quite provide all the results needed in their quest for a better competitive posture. A lot of those organizations have found that by combining Lean with Six Sigma, significant performance gains relative to processes, products, services, employees, customer satisfaction, and the business bottom line have been realized.
Lean and Six Sigma complement each other with their strengths, namely Lean’s elimination of waste and Six Sigma’s breakthrough methodology for solving performance problems and making improvements, DMAIC, and its infrastructure system of Belts.
Advantages of Lean Six Sigma include:
-
Elimination of the Eight Wastes—waiting, overproduction, rework, motion, transportation, processing, inventory, and intellect
-
Means of improving process flow whether on the manufacturing floor, in an office, or any other setting
-
A structured means for identifying the key factors that determine the performance of all kinds of processes
-
Ordered methods for establishing key factors at the best possible level
-
Disciplined means of sustaining key factors at the best level
-
Synergistic advantage of linking the Lean tools with the Six Sigma tools in a systematic way and in a specified sequence
-
Trying all of these to the financial health of the organization
Q6. Define benchmarking.
ANS: Benchmarking is the process of comparing and measuring an organization’s operations or its internal processes against those of a best-in-class performer from inside or outside its industry. Benchmarking is finding the secrets of success of any given function or process so that a company can learn from the information—and improve on it. It is a process to help a company close the gap with the best-in-class performer without having to “reinvent the wheel.”
Q7. How can you apply benchmarking data?
ANS: At the conclusion of the benchmarking project with your partner, data analysis will have produced both quantitative and qualitative information. The quantitative information is effectively the “stake driven into the ground” as the point from which future progress is measured. It is also used as the basis for improvement objectives. Qualitative information covers such matters as personnel policies, training, management styles and hierarchy, total quality maturity, and so on. This information provides insights on how the benchmarking partner got to be best-in-class.
The quantitative data are clearly the information sought and are always used. However, there may be more value in the qualitative information. It describes the atmosphere and environment in which best-in-class can be developed and sustained. Do not ignore it. Take it very seriously. Study it, discuss it in staff meetings, and explore the possibilities of introducing these changes into your culture.
The benchmarking process is shown in the figure below.
Q8. What is a JIT system?
ANS: This manufacturing system was initially developed by Taiichi Ohno in the 1950s as the successor to Henry Ford’s mass production system. Ohno named it theToyota Production System (TPS). Since it involved making products only when needed from materials that were made available by suppliers only as required,just-in-time (JIT) became its generic name.
Just-in-time/Lean is producing only what is needed, when it is needed, and in the quantity that is needed. It approaches the manufacturing process from the opposite end of the line. Rather than pushing materials into the processes and storing them whenever they cannot be accommodated, JIT/Lean controls the line from the output end. Indeed, it can be said that the customer controls the line because nothing is built until there is an order for it.
Q9. What are the benefits of JIT/lean?
ANS: Mass production manufacturers set their production schedules based on a forecast of future needs, which, in turn, is based on historical data and trend analysis. The great weakness of this system is that no one can predict the future with sufficient certainty, even with a complete and perfect understanding of the past and a good sense of current trends in the marketplace. The result of JIT/ Lean is that no goods are produced without demand. This, in turn, means no goods are produced that cannot be sold at a price that supports the viability of the company.
If we look at a complete production process, we will find that it contains many producers and customers—internal producers and customers. Each preceding process in the overall system is a producer, or supplier, and each succeeding process is a customer. JIT/Lean fits here as well as or better than with the manufacturer-and-purchaser model. No process in the system produces its output product until it is signaled to do so by the succeeding process. This can eliminate waste on a grand scale. It is the elimination of waste that justifies JIT/Lean in any kind of manufacturing operation. Eliminating waste is translated into improving quality and lowering costs. Improving quality and lowering costs translate into becoming more competitive. Although improving competitiveness does not assure survival (the competition may still be ahead of you), being noncompetitive surely guarantees disaster.
Taiichi Ohno, the creator of the just-in-time/Lean system, saw that the mass production system produced waste at every step. He identified seven wastes:
-
Overproducing
-
Waiting (time)
-
Transporting
-
Processing itself
-
Having unnecessary stock on hand
-
Using unnecessary motion
-
Producing defective goods
The elimination of these wastes is at the heart of the rationale for just-in-time/Lean: eliminate these wastes, and you will produce better products at lower cost. If the competition gets there first, your rationale for JIT/Lean is survival.
Q10. Discuss automation system ideas for JIT/lean.
ANS: It is frequently found that the need for automation is decreased or eliminated by converting to JIT/Lean. JIT/Lean and automation are compatible, but one should look long and hard at the need, and the company’s readiness for it, before automating processes.
Having said that, automation clearly has its place in harmony with JIT/Lean. There are many examples of very successful automated plants, especially for high-volume manufacturing. Automation and JIT/Lean are completely compatible. Probably the best example of that is in today’s auto industry. Two such plants have recently come on-line in Alabama and Georgia. Hyundai opened its first American plant in Montgomery, Alabama, in May 2005, making 300,000 vehicles per year there. The Alabama-produced Sonata sedan has been ranked in the top three in J. D. Power and Associates’ mid-size sedan category in 2008, 2009, and 2010. This plant is one of the first designed from the ground up as a highly automated JIT/Lean auto production facility. A tour of the plant will convince the fervent skeptic that it has taken the auto industry into a new era in which JIT/Lean and automation are superbly blended. Where traditional auto plants tended to be dark, noisy, grimy, smelly, hot, and frantic in the hustle and bustle, Hyundai’s Montgomery plant is none of that. No matter where you are in the plant, the atmosphere is almost soothing, and it is certainly one of the most pleasant factories of any type that the authors have ever visited. It is a place where the 2,300 employees genuinely seem to enjoy working. And it doesn’t end there. An hour from Montgomery, up Interstate 85 in West Point, Georgia, Kia Motors opened a sister plant of the same size and capacity, using the same automation technology and, of course, JIT/Lean. The first Kia Sorento rolled off that line in November 2009.
SOCIAL NETWORKING ARTICLES SUMMARY:
Executive Summary 1: Practice Makes a Career
"Consider that first occupation important, and you never know where it can lead!" Professor Bernard J. Tyson expressed while giving a moving message to youthful interns.He advised how he grew up to the position of CEO of Kaiser Permanente. The method is straightforward, he says,practice your picked profession.He told how entry level positions are the most vital step that gives us the chance to show our aptitudes, our energy , inspiration and knowledge.To utilize the time well to be perceived as a potential representative is another key he gave.He supported by telling that each individual can possibly turn into a future pioneer or contributor.Improve continually. Search out individuals why should willing tutor and show you. Express your right to speak freely furthermore comprehend your commitments, says Mr. Tyson"Communications, innovation, bookkeeping, or more", persuades Mr. Tyson, "After some time, your devotion to honing will appear, and you will be more certain about — and regarded for — your demonstrated range of skill."
Executive Summary 2: Microsoft acquires Minecraft app for schools
In 2014 Microsoft has obtained the maker of the diversion Minecraft and this in a split second got a catch with youngsters and made a blockbuster amusement application for an era that did not rely on upon the different items the way their folks did. They had expected to utilize the MinecraftEdu altered form in the different classrooms of schools to make educating and taking in an all-new ordeal. It has pulled in a solid after and is utilized as a part of more than 7,000 classrooms in more than 40 nations. This innovative instrument is being utilized to show earth science, math, et cetera. Various lessons are taught in creative better ways to deal with manufacture cognizance of understudies. Regardless of the way that Minecraft is immensely surely understood no affirmation has been appeared with reference to how Microsoft has been benefitted from this entire arrangement. Microsoft has some understood apparatuses before that have been utilized, for instance, PowerPoint, One Note and Skype. In this engaged environment, Microsoft courses of action to charge $5 per understudy each year and offer social event markdown. Disregarding every one of this, the application would achieve another way to deal with the entire learning knowledge for the youngsters and looking onto the upsides of this application for the not so distant future eras and in addition the organization wanting to pick up a benefit from this entire arrangement.
Executive Summary 3: Tough times ahead for Tesla and Elon Musk
In 2006, Elon Musk laid out his representation for his everything electric auto organization in a blog entry promising all-electric extravagance autos would be succeeded by expanding reasonable every single electric vehicle. Presently, this year in March, Elon Musk took to stage to reveal Model 3 and even before he divulged the auto, Tesla as of now had 115,000 individuals saved $1000 to arrange the auto two years before it is accessible. Not even a month since the dispatch, plainly Tesla as of now has a colossal hit staring its in the face. Elon Musk recently declared that the reservations are achieving more like 400,000.
The primary question that emerges now is that whether Tesla can convey the auto on time, in the past Tesla has neglected to convey purposeful due dates. 400,000 requests would be difficult to satisfy since Tesla just created 50,000 autos in 2015. So it is difficult to concoct 400,000 autos in a year or two. Tesla wanted to build the generation from 50K to 500K autos every year and this would expand quality issues profoundly. Tesla has a considerable measure to convey with the Model 3 and in the event that they neglected to convey quality autos on time, then this is going to harm the brand.

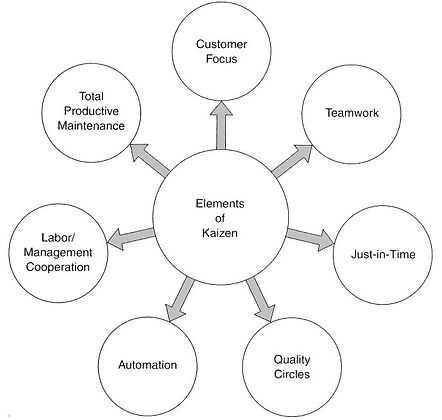